Introduction: Navigating the Tapestry of T-Shirt Printing
In the dynamic world of fashion, the humble T-shirt stands as an iconic canvas waiting to be transformed into a wearable masterpiece. The artistry of T-shirt printing has evolved far beyond simple logos or slogans, becoming a vibrant means of self-expression and creativity. As we embark on this journey through the realm of T-shirt printing, we’ll unravel the intricacies of various printing techniques that contribute to the kaleidoscope of designs adorning our everyday apparel.
T-Shirt Printing: A Canvas of Creativity
The significance of T-shirt printing extends beyond mere fabric embellishment; it encapsulates the fusion of art, technology, and personal expression. The ability to imprint unique designs onto a T-shirt opens the door to a world where individuality takes center stage. From bold graphics and intricate patterns to personalized messages, T-shirt printing allows wearers to showcase their personality and style.
The Diverse Landscape of Printing Techniques
The landscape of T-shirt printing is rich and diverse, with each technique offering a unique set of advantages and artistic possibilities. From traditional methods rooted in craftsmanship to cutting-edge technologies that leverage digital precision, the world of T-shirt printing is a tapestry woven with threads of innovation and creativity.
Embarking on a Guided Exploration
As we embark on this guided exploration, we will delve into the most popular T-shirt printing techniques, dissecting their processes, strengths, and potential applications. From the timeless artistry of silk screen printing to the modern precision of direct-to-garment (DTG) printing, each method contributes to the expansive palette of choices available to designers and creators.
Empowering the Creators
This comprehensive guide aims to empower creators, designers, and enthusiasts to navigate the complex landscape of T-shirt printing with confidence. Whether you’re a seasoned professional or a budding artist, understanding the nuances of each printing technique will enable you to make informed decisions, turning your design concepts into tangible, wearable art.
Join us on this Journey
So, join us on this journey through the diverse world of T-shirt printing. Uncover the secrets of various printing methods, explore their applications, and gain insights into choosing the right technique for your unique design vision. As we navigate this tapestry of T-shirt printing, let’s celebrate the boundless creativity that transforms a simple piece of fabric into a statement of individuality and style.
Most Popular T-Shirt Printing Types: A Spectrum of Choices
When it comes to T-shirt printing, the methods employed are as diverse as the designs they bring to life. From traditional techniques that have withstood the test of time to cutting-edge technologies that redefine the boundaries of creativity, the world of T-shirt printing is a vibrant spectrum of choices. Let’s explore the most popular types, each adding its unique hue to the canvas of personalized apparel.
1. Direct-to-Garment (DTG) Printing: Merging Precision with Color Variety
Process Overview: Direct-to-Garment printing, or DTG, is a modern method that involves using specialized inkjet printers to apply full-color designs directly onto the fabric. This process is akin to printing a digital image on paper but tailored for clothing.
Advantages:
- Supports intricate designs with a high level of detail.
- Ideal for vibrant, multicolored prints.
- Suited for small-batch or one-off designs.
Considerations:
- Best on 100% cotton garments for optimal results.
- May have limitations on dark-colored fabrics.
2. Screen Printing: A Timeless Craft with Artisanal Precision
Process Overview: Screen printing, a classic and widely-used technique, involves creating a stencil (screen) for each color in the design. Ink is then pushed through the screens onto the fabric, layer by layer, forming the final design.
Advantages:
- Suitable for large production runs.
- Offers durability and long-lasting prints.
- Ideal for bold, simple designs.
Considerations:
- Set-up costs may be higher for multiple colors.
- Detailed designs may require higher screen mesh counts.
3. Heat Transfer Methods: Versatility in Application
3.1 Heat Transfer Vinyl (HTV): Process Overview: HTV involves cutting designs from colored vinyl sheets and heat-pressing them onto the fabric. This method is popular for single-color or multicolored designs.
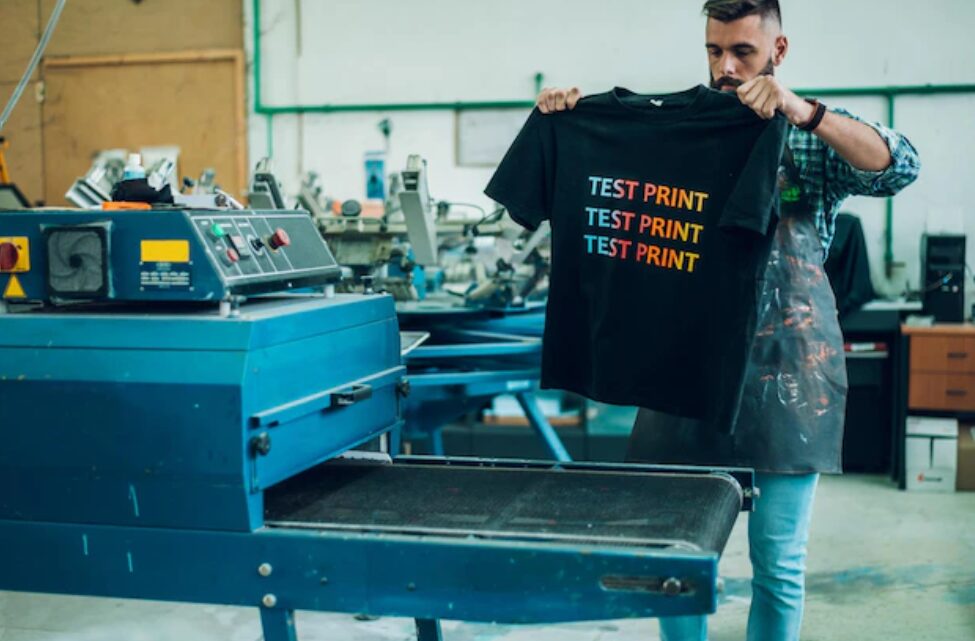
Advantages:
- Suitable for detailed designs and lettering.
- Durable and long-lasting prints.
Considerations:
- Not ideal for intricate, multicolored designs.
3.2 Sublimation Printing: Process Overview: Sublimation printing uses heat to transfer dye onto the fabric, resulting in vibrant and full-color designs. It’s particularly effective on polyester garments.
Advantages:
- Allows for all-over printing.
- Produces durable and fade-resistant prints.
Considerations:
- Limited to polyester or polyester-coated items.
4. Embroidery: Textured Elegance for a Timeless Appeal
Process Overview: Embroidery involves stitching thread into the fabric to create raised designs. It adds a tactile and sophisticated dimension to T-shirts.
Advantages:
- Offers a premium, textured finish.
- Long-lasting and visually appealing.
Considerations:
- More suitable for simple logos or text.
5. Digital Transfer Printing: Combining Detail and Color Range
Process Overview: Digital transfer printing involves creating a design digitally and then transferring it onto the fabric using heat. This method allows for intricate designs and a wide color range.
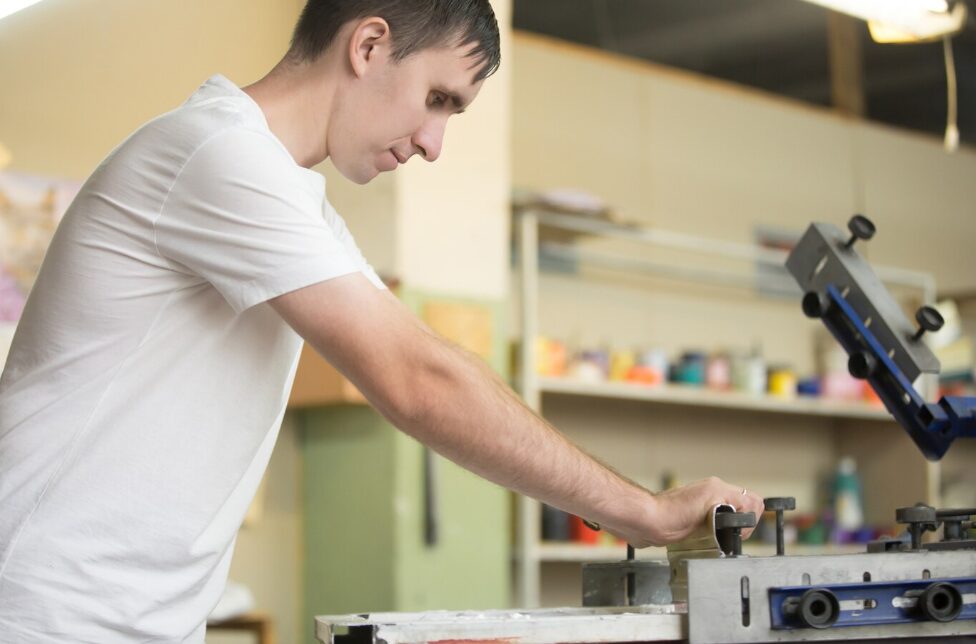
Advantages:
- Ideal for detailed and colorful designs.
- Works well on various fabrics.
Considerations:
- Quality may vary based on transfer paper used.
Choosing Your Palette of Possibilities
Each T-shirt printing method outlined above brings its own set of advantages and considerations. The choice depends on factors like the complexity of your design, the type of fabric, and the desired quantity. As we navigate the diverse landscape of T-shirt printing, the next segments will delve deeper into each method, providing insights to help you make an informed decision. Whether you’re aiming for precision, durability, or artistic versatility, there’s a printing type that aligns with your vision. Stay tuned to discover the artistry behind each technique, guiding you towards the perfect choice for your personalized apparel creations.
Direct-to-Garment Printing (DTG): Merging Precision with Detail
In the realm of T-shirt printing, Direct-to-Garment (DTG) stands out as a contemporary marvel, seamlessly merging precision and vivid detail to bring designs to life on fabric. This method, often referred to as digital garment printing, has gained immense popularity for its ability to reproduce intricate designs with a full spectrum of colors. Let’s take a closer look at the art and science behind DTG printing.
Process Overview: Unveiling the Digital Tapestry
1. Design Preparation: DTG printing begins with a digital design file, much like a high-resolution image. Whether it’s a complex artwork or a detailed photograph, the digital nature of the design sets the stage for a seamless printing process.
2. Pre-Treatment: Before the magic of printing happens, the fabric undergoes a pre-treatment process. This involves applying a special solution to the garment, enhancing the absorption of the ink. Proper pre-treatment is crucial for achieving vibrant and lasting prints.
3. Printing: The treated garment is loaded onto the DTG printer, which resembles a traditional inkjet printer but on a larger scale. The printer precisely applies water-based inks directly onto the fabric, penetrating the fibers to create a seamless integration of design and material.
4. Curing: Once the printing is complete, the T-shirt goes through a curing process. This involves heat-pressing the garment to set the inks. Curing ensures the durability and wash-fastness of the print, making it a lasting addition to the fabric.
Advantages of DTG Printing: Unlocking a Palette of Possibilities
- High Detail Reproduction: DTG excels at capturing intricate details with remarkable precision. Fine lines, gradients, and even photorealistic images can be faithfully reproduced, making it a preferred choice for designs with elaborate elements.
- Full-Color Spectrum: Unlike some traditional printing methods that may have color limitations, DTG allows for the use of a full spectrum of colors. This makes it an ideal choice for designs with multiple hues and shades.
- No Setup Costs for Color Changes: Traditional methods like screen printing may incur setup costs for each color used. DTG eliminates this concern; you can print a rainbow of colors without worrying about additional expenses.
- Perfect for Small Batches: DTG’s digital nature makes it highly suitable for small production runs or even one-off prints. This flexibility caters to the growing demand for personalized and unique apparel.
- Soft Feel on Fabric: The water-based inks used in DTG printing are absorbed into the fabric, resulting in a soft and comfortable feel. The print becomes an integral part of the garment, maintaining its natural texture.
Considerations for DTG Printing: Fine-Tuning the Canvas
- Optimal on 100% Cotton: While DTG can be used on various fabrics, it performs optimally on 100% cotton garments. The natural fibers allow for better ink absorption, enhancing the vibrancy of the print.
- Dark Garments May Pose Challenges: Achieving vibrant prints on dark-colored garments can be challenging with DTG. Pre-treatment and multiple passes may be required, impacting the overall feel of the print.
- Upfront Investment: While DTG offers advantages in terms of color range and detail, the initial investment in a quality DTG printer can be significant.
Conclusion: Elevating Personalized Apparel
Direct-to-Garment printing emerges as a game-changer in the landscape of T-shirt customization. Its ability to faithfully reproduce intricate designs and offer a full range of colors makes it a go-to choice for those seeking precision and versatility. As we explore further into the tapestry of T-shirt printing, each method adds its unique strokes to the canvas, contributing to the rich diversity of personalized apparel creation. Stay tuned for the next segment, where we unravel the artistry behind another popular printing method, Screen Printing, unveiling its timeless appeal and unique characteristics.
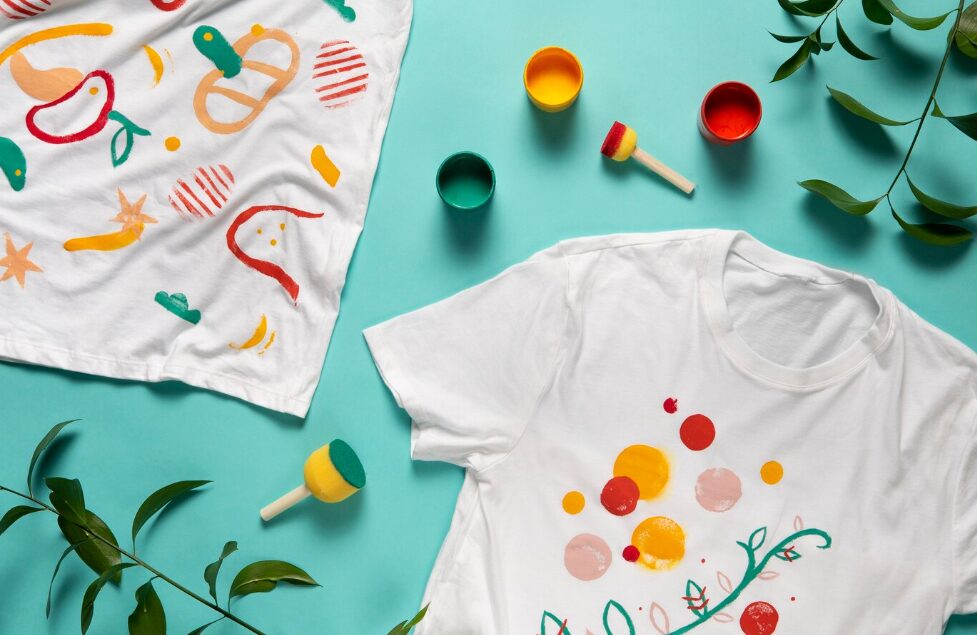
Screen Printing: Timeless Craftsmanship
In the ever-evolving landscape of T-shirt printing, there’s a method that stands as a beacon of timeless craftsmanship — Screen Printing. This traditional technique has adorned garments with its unique charm for decades, becoming synonymous with durability, vibrancy, and a touch of artisanal flair. Let’s delve into the art and intricacies of screen printing.
The Art of Screen Printing: A Storied Process
1. Design Transference: At the heart of screen printing lies the stencil, a mesh screen treated with an impermeable substance. The design is transferred onto this screen, leaving the negative space open for ink to pass through. Each color in the design requires a separate screen.
2. Preparing the Screen: Once the design is in place, the screen is prepared with the chosen ink color. The impermeable substance ensures that ink can only pass through the designated areas, creating a sharp and defined print.
3. The Printing Process: Positioned over the garment, the screen is lowered, and ink is applied to the top of the screen. A squeegee is then used to evenly distribute the ink across the screen, pushing it through the open mesh and onto the fabric beneath. This process is repeated for each color, with precise registration to ensure a cohesive design.
4. Curing the Ink: To make the print permanent, the garment goes through a curing process. It involves applying heat to set the ink into the fabric, ensuring longevity and wash-fastness.
Advantages of Screen Printing: Crafted Excellence
- Durability: Screen printing is renowned for its durability. The thick layers of ink applied during the process result in prints that withstand the test of time, making it a preferred choice for workwear, team uniforms, and promotional items.
- Vibrancy on Dark Fabrics: Unlike some other methods, screen printing excels on dark-colored fabrics. The ability to apply multiple layers of opaque ink ensures vivid and eye-catching prints on various garment colors.
- Cost-Effective for Bulk Orders: Screen printing becomes cost-effective with larger quantities. Once the screens are set up, the process becomes more efficient, making it an economical choice for bulk orders.
- Versatility in Inks: Screen printing offers versatility in ink types, including metallic and specialty inks. This allows for creative expression and customization beyond standard colors.
- Ideal for Simple and Bold Designs: Bold, simple designs find their perfect medium in screen printing. The method excels at reproducing clean lines, solid colors, and designs with strong contrasts.
Considerations for Screen Printing: Crafting Excellence
- Setup Costs for Multiple Colors: Screen printing involves separate screens for each color in the design. This can result in setup costs, making it less economical for designs with numerous colors, especially in smaller orders.
- Detailed Designs May Pose Challenges: While screen printing is excellent for bold and simple designs, intricate details may not be as accurately reproduced. Fine lines and small text can be challenging to capture.
- Not Ideal for Small Runs: The setup involved in screen printing makes it less suitable for small production runs. It truly shines when catering to larger quantities.
Conclusion: Embracing Tradition in Modern Apparel
Screen printing, with its rich history and undeniable charm, continues to hold a special place in the world of T-shirt printing. Its ability to deliver vibrant and durable prints, especially on dark fabrics, showcases the craftsmanship that goes into each garment. As we explore the diverse techniques in T-shirt printing, screen printing stands as a testament to the marriage of tradition and innovation, offering a canvas for timeless designs to come to life. Stay tuned for the next segment, where we unravel the intricacies of another printing method, Heat Transfer Printing, unveiling its unique characteristics and applications in the world of personalized apparel.
Heat Transfer Methods: Bringing Designs to Life
In the vibrant tapestry of T-shirt printing, Heat Transfer Methods emerge as a versatile and accessible technique, offering a bridge between precision and personalization. Let’s explore the intricacies of this method, where designs come to life through the transformative power of heat.
Understanding Heat Transfer Printing: A Fusion of Art and Science
1. The Basics: Heat Transfer Printing involves applying a design to a garment using heat and pressure. This method is widely employed for its ability to reproduce intricate details and full-color designs with ease.
2. Types of Heat Transfer:
- Vinyl Heat Transfer: Vinyl sheets, cut into the desired design, are heat-pressed onto the fabric. This method is popular for its durability and the option to use various vinyl types, including glitter and metallic.
- Sublimation Heat Transfer: Using heat-sensitive inks, the design is transferred onto a special sublimation paper. Through heat and pressure, the ink transforms into a gas and permeates the fabric, resulting in vivid, permanent prints.
- Plastisol Transfers: Designs are screen-printed onto a special release paper using plastisol ink. When heat is applied, the ink releases from the paper and adheres to the fabric, creating a durable and detailed print.
3. The Transfer Process:
- Design Creation: Designs are either digitally printed or cut from heat-transfer materials.
- Heat Press Application: The designed material is placed on the garment, and a heat press is used to apply heat and pressure. The combination of these elements activates the adhesive in the design, securing it to the fabric.
Advantages of Heat Transfer Printing: Precision and Diversity
- Intricate Detailing: Heat transfer excels at capturing intricate details and complex designs, making it suitable for reproducing artworks, photographs, and fine patterns.
- Full-Color Reproduction: Unlike some traditional methods, heat transfer allows for full-color printing. This is particularly advantageous when dealing with designs that demand a broad spectrum of hues.
- Ideal for Small Runs: Heat transfer methods are cost-effective for small production runs. There’s minimal setup, making it a feasible choice for customized and on-demand printing.
- Application on Various Fabrics: From cotton and polyester to blends, heat transfer printing is versatile and can be applied to a wide range of fabrics, expanding the possibilities for personalized apparel.
- Quick Turnaround: The straightforward process of heat transfer leads to a quicker turnaround time, making it a suitable choice for time-sensitive projects.
Considerations for Heat Transfer Printing: Tailoring to Your Needs
- Durability on Certain Fabrics: While suitable for various fabrics, the durability of heat transfer prints can vary. It may not withstand the same level of wear and washing as some other methods, especially on fabrics prone to frequent stretching.
- Feel of the Print: Heat transfer prints may have a different feel on the fabric compared to traditional screen prints. This aspect is subjective and depends on personal preferences.
- Cost for Larger Runs: In comparison to methods like screen printing, heat transfer printing can become more costly for larger production runs due to the cost of materials.
Conclusion: Unleashing Creative Potential with Heat Transfer
As we unravel the diverse methods in T-shirt printing, Heat Transfer emerges as a powerhouse for precision and diversity. Its ability to bring intricate designs to life, coupled with the versatility to work on various fabrics, makes it a sought-after choice for personalized apparel. Join us in the next segment as we delve into the realm of Full Dye Sublimation, exploring its unique characteristics and applications in the world of customized garment creation.
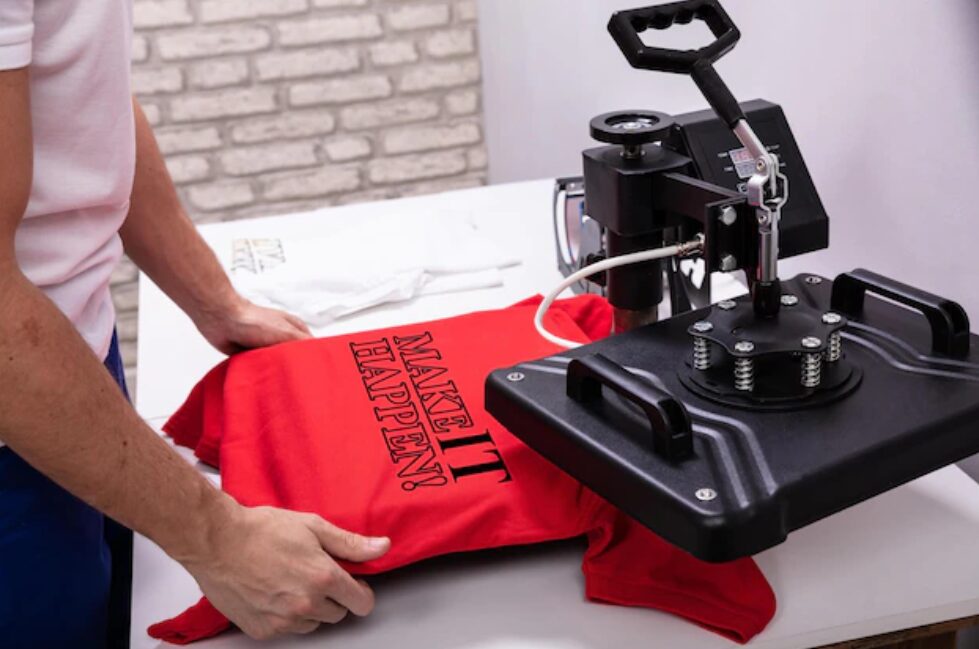
Dye Sublimation or All-Over Printing (AOP): A Canvas of Infinite Possibilities
In the dynamic landscape of T-shirt printing, the artistry reaches new heights with Dye Sublimation or All-Over Printing (AOP). This technique transforms garments into a canvas of infinite possibilities, offering a seamless blend of vibrant colors and unrestricted creativity.
Understanding Dye Sublimation: The Alchemy of Color and Fabric
1. The Essence of Dye Sublimation: Dye sublimation is a unique printing process that involves transferring designs onto fabric using heat and special inks. Unlike traditional methods, the ink transitions directly from a solid to a gas without entering a liquid state. This transformative process ensures a more extended life for the print.
2. The Sublimation Process:
- Design Preparation: Designs are digitally created, often with vibrant and intricate patterns that extend across the entire garment.
- Printing on Special Paper: The design is printed onto a special sublimation paper using sublimation inks.
- Heat Transfer: The paper with the design is placed on the fabric, and heat is applied using a heat press. The heat causes the inks to turn into gas, permeating the fabric and resulting in a full-color, continuous print.
Advantages of Dye Sublimation: Unmatched Creativity and Durability
- Unrestricted Design Possibilities: Dye sublimation enables the creation of intricate, full-color designs that cover the entire garment. This technique is perfect for those seeking to unleash their creative visions without limitations.
- Vibrant and Long-Lasting Colors: The colors produced through sublimation are exceptionally vibrant and durable. The prints withstand washing and maintain their brilliance over time, making them ideal for activewear and vibrant fashion statements.
- Breathable and Comfortable Prints: Since the ink becomes a part of the fabric rather than sitting on top, sublimation prints are breathable and do not compromise the fabric’s comfort. This is particularly beneficial for sportswear and apparel worn in warmer climates.
- End-to-End Design Coverage: AOP allows for complete design coverage from seam to seam, offering a visually impactful result. This is perfect for creating unique and eye-catching garments that stand out.
- Complex and Photographic Reproduction: Dye sublimation excels in reproducing intricate details and photographic elements. This makes it a preferred choice for those aiming to showcase detailed artworks or intricate patterns.
Considerations for Dye Sublimation Printing: Tailoring to Your Needs
- Fabric Selection: While sublimation works well on polyester fabrics, it may not be suitable for natural fibers like cotton. The process requires a high polyester content for optimal results.
- Limitations on Dark Colors: Sublimation tends to work better on lighter-colored fabrics, as the colors may not be as vibrant on dark backgrounds. Design considerations should account for the base color of the garment.
- Ideal for Polyester Blends: Fabrics with a higher polyester blend yield the best results with sublimation. It’s essential to choose fabrics that align with the desired outcome.
Conclusion: AOP – Where Every Inch Becomes a Canvas
Dye Sublimation or All-Over Printing stands at the forefront of T-shirt printing, providing a canvas where every inch becomes a realm of creative expression. The seamless fusion of vibrant colors and unrestricted design possibilities positions AOP as a powerful technique for those seeking to make a bold statement through their garments. Join us in the next segment as we explore the realm of Direct Film Printing (DTF), delving into its unique characteristics and applications in the realm of personalized apparel.
Direct-to-Film Printing (DTF): Bridging Precision and Versatility
As we continue our exploration of T-shirt printing techniques, we delve into the realm of Direct-to-Film Printing (DTF). This method stands as a bridge between precision and versatility, offering a unique approach to transferring intricate designs onto garments.
Unveiling Direct-to-Film Printing: A Marriage of Precision and Versatility
1. The Core of DTF Technology: Direct-to-Film Printing involves the creation of a design on a transparent film, which is then transferred to the fabric using a combination of heat and pressure. This method provides a precise and detailed print, making it suitable for complex and intricate artworks.
2. The DTF Process:
- Design Creation: Digital designs are crafted with meticulous attention to detail, incorporating intricate patterns or fine details.
- Film Printing: The design is printed onto a special film using specific DTF printers and inks.
- Film Transfer: The printed film is carefully placed on the garment, and a heat press is utilized to transfer the design from the film to the fabric.
Advantages of DTF: Precision Meets Flexibility
- High Precision and Detail: DTF excels in reproducing intricate details and complex designs with precision. Fine lines, small text, and elaborate patterns are captured accurately in the transfer process.
- Versatility in Fabric Selection: Unlike some other methods that are limited to specific fabric types, DTF can be applied to various fabrics, including cotton, polyester, and blends. This versatility opens up possibilities for a broader range of garment choices.
- Full-Color Spectrum: DTF supports a full-color spectrum, allowing for vibrant and detailed designs. This makes it an excellent choice for those looking to bring colorful and intricate artwork to life on their garments.
- Adaptability to Dark Fabrics: DTF performs well on both light and dark fabrics, providing flexibility in design choices. The process ensures that colors remain vivid even on darker backgrounds.
- Durability and Wash Resistance: The prints created through DTF are known for their durability and resistance to fading during washing. This ensures that the garment maintains its vibrant appearance even after multiple wash cycles.
Considerations for DTF Printing: Customization with Precision
- Film Quality Matters: The quality of the film used in DTF significantly impacts the final result. High-quality films contribute to better detail transfer and overall print quality.
- Versatility Across Fabrics: While DTF is versatile across various fabrics, it’s essential to consider the fabric’s composition to achieve optimal results. Some fabrics may require specific pre-treatment processes.
- Complexity of Designs: DTF is particularly suitable for designs with intricate details and complex patterns. If your design involves fine lines or detailed artwork, DTF can capture these elements with precision.
Conclusion: Precision Unleashed with DTF
Direct-to-Film Printing emerges as a powerful tool in the T-shirt printing arsenal, combining precision and versatility. Its ability to handle intricate designs with finesse, coupled with adaptability to various fabrics, positions DTF as a go-to method for those seeking a balance between detailed artistry and customization. Join us in the next segment as we unravel the world of Plasticol Transfer, exploring its characteristics and applications in the realm of personalized apparel.
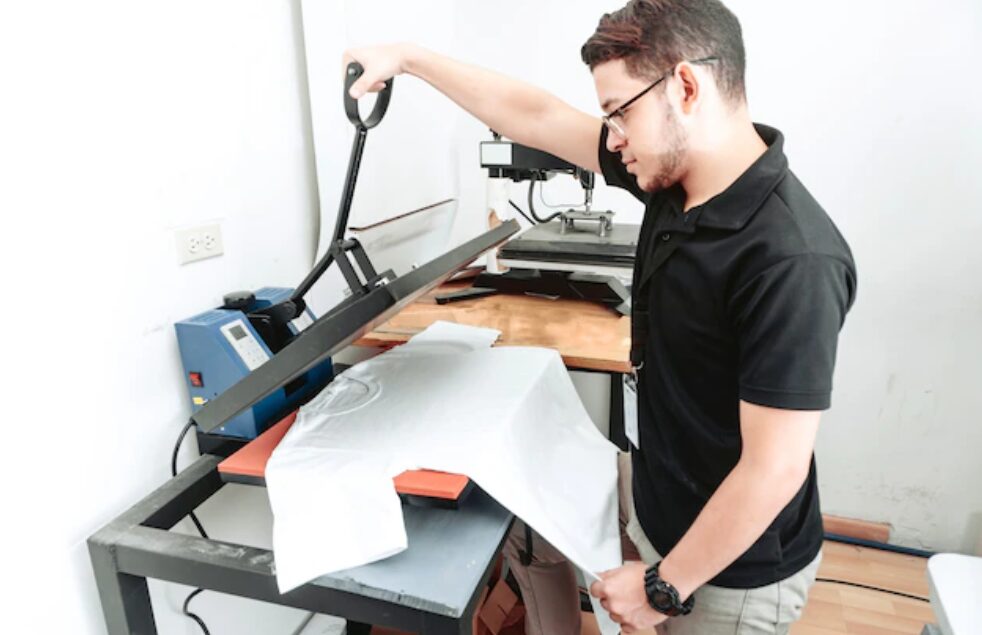
Plastisol Transfer: The Art of Precision
In our exploration of T-shirt printing methods, we arrive at the technique known as Plastisol Transfer. This method represents the art of precision, offering a versatile and efficient way to transfer detailed designs onto garments.
Understanding Plastisol Transfer: A Fusion of Precision and Flexibility
1. The Essence of Plastisol Ink: At the heart of Plastisol Transfer lies the use of Plastisol ink, a PVC-based ink renowned for its vibrant colors and durability. This ink serves as the medium for creating intricate designs that can be precisely transferred to garments.
2. The Plastisol Transfer Process:
- Design Creation: Digital designs are crafted, paying close attention to details and color composition.
- Ink Printing: The design is printed onto a special release paper using Plastisol ink.
- Heat Transfer: The printed design on the release paper is placed on the garment, and heat is applied using a heat press. The heat causes the Plastisol ink to liquefy and bond with the fabric, resulting in a permanent and detailed print.
Advantages of Plastisol Transfer: Precision and Versatility Combined
- Detail Precision: Plastisol Transfer excels in reproducing intricate details and fine lines. This makes it an ideal choice for designs that demand precision, such as intricate artworks or detailed logos.
- Vibrant Colors: Plastisol ink offers a wide range of vibrant colors. The colors remain vivid even after the transfer process, contributing to the visual appeal of the final print.
- Consistency in Quality: The use of Plastisol ink and the controlled heat transfer process contribute to consistent print quality. This reliability is crucial for achieving a professional and polished appearance across a batch of printed garments.
- Versatility Across Fabrics: Plastisol Transfer is versatile and compatible with various fabric types, including cotton, polyester, and blends. This adaptability allows for a diverse range of garment choices.
- Durability and Wash Resistance: The prints created through Plastisol Transfer are known for their durability and resistance to fading during washing. This ensures that the garment maintains its vibrant appearance over time.
Considerations for Plastisol Transfer: A Balance of Art and Application
- Heat Press Settings: Achieving the right balance of heat and pressure during the transfer process is crucial for optimal results. Proper heat press settings ensure that the Plastisol ink bonds effectively with the fabric.
- Release Paper Quality: The quality of the release paper used for printing the design plays a role in the transfer process. High-quality release paper contributes to better ink transfer and overall print quality.
- Color Matching: Given the vibrant color options of Plastisol ink, attention to color matching is essential for maintaining design integrity. Consistency in color across prints enhances the overall visual impact.
Conclusion: Precision and Durability with Plastisol Transfer
Plastisol Transfer emerges as a technique that brings precision and versatility to T-shirt printing. Its ability to capture intricate details, coupled with vibrant color options and durability, makes it a preferred choice for those seeking a balance between artistry and reliability. Join us in the next segment as we explore CAD Heat Transfer Vinyl Printing, unraveling its characteristics and applications in the landscape of personalized apparel.
CAD Heat Transfer Vinyl Printing: Precision in Personalization
As we continue our journey through the diverse realm of T-shirt printing methods, we arrive at CAD Heat Transfer Vinyl Printing, a technique that combines precision and personalization. This method empowers creators to achieve detailed and customized designs with accuracy.
Understanding CAD Heat Transfer Vinyl Printing: Melding Technology with Creativity
1. The Essence of CAD Heat Transfer Vinyl: At the core of this method is the use of CAD (Computer-Aided Design) Heat Transfer Vinyl. This vinyl material is specially designed for heat transfer applications, providing a canvas for intricate designs and precise customization.
2. The CAD Heat Transfer Process:
- Design Creation: Digital designs are crafted using computer software, allowing for intricate details and personalized elements.
- Vinyl Cutting: The designed image is translated into a vector file, guiding a cutting machine to precisely cut the pattern onto the CAD Heat Transfer Vinyl sheet.
- Weeding: Unwanted vinyl portions are manually removed, leaving only the intended design on a carrier sheet.
- Heat Transfer: The cut vinyl design, still attached to the carrier sheet, is heat-pressed onto the garment. The heat activates the adhesive on the vinyl, bonding it securely to the fabric.
Advantages of CAD Heat Transfer Vinyl Printing: Precision and Customization Unleashed
- Precision in Detail: CAD technology ensures precise cutting of intricate designs, enabling the reproduction of fine lines, small text, and intricate patterns.
- Personalization Possibilities: This method excels in personalized designs. From individual names to unique graphics, CAD Heat Transfer Vinyl Printing offers a high level of customization.
- Versatility Across Fabrics: CAD Heat Transfer Vinyl adheres well to various fabric types, including cotton, polyester, and blends. This versatility expands the range of garments that can be personalized using this method.
- Durability and Longevity: The heat-pressed vinyl creates a durable bond with the fabric, resulting in a long-lasting print. The prints withstand regular washing and maintain their quality over time.
- Color Variety: CAD Heat Transfer Vinyl is available in a wide array of colors, including specialty finishes like metallic or fluorescent. This color variety allows for creative expression and design flexibility.
Considerations for CAD Heat Transfer Vinyl Printing: Mastering the Craft
- Vector Design Precision: The quality of the final print heavily relies on the precision of the vector design. Attention to detail during the design phase ensures accurate cutting and weeding.
- Weeding Expertise: Skillful weeding is essential for removing excess vinyl while preserving the integrity of the design. This meticulous process contributes to the final visual impact.
- Heat Press Settings: Achieving the right temperature and pressure during the heat transfer process is crucial. Proper settings ensure optimal adhesion without damaging the vinyl or the fabric.
Conclusion: Precision Meets Personalization with CAD Heat Transfer Vinyl Printing
In the tapestry of T-shirt printing methods, CAD Heat Transfer Vinyl Printing stands out as a blend of precision and personalization. The marriage of technology-driven cutting accuracy and creative customization makes this method a go-to choice for those seeking to infuse their garments with unique, detailed designs. Join us in the upcoming segment as we delve into the realm of Other Printing Technologies, uncovering unconventional yet fascinating approaches to personalized apparel.
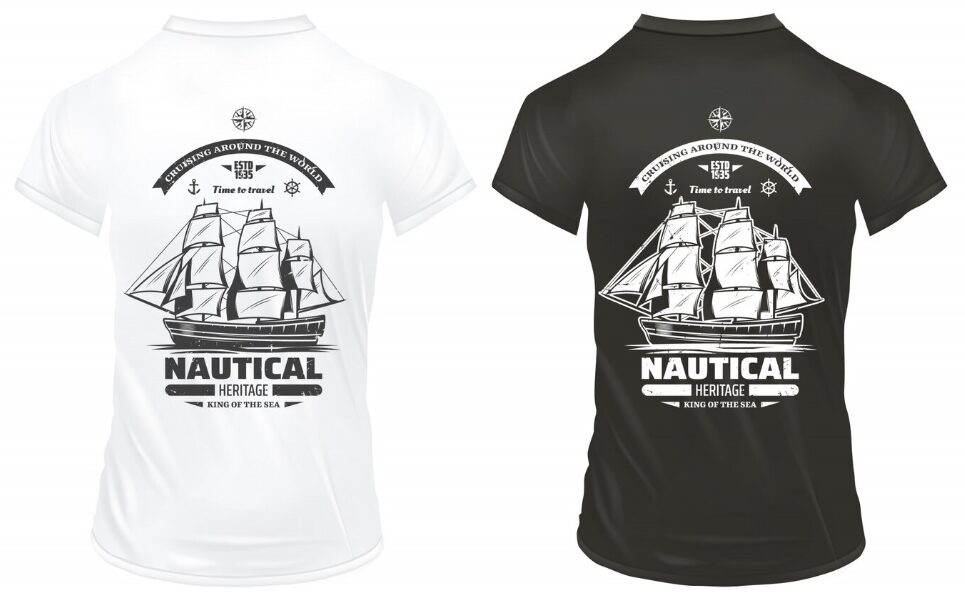
Other Printing Technologies: Beyond the Basics
As we traverse the expansive landscape of T-shirt printing, we unveil a realm of innovation and uniqueness encapsulated in Other Printing Technologies. These methods, while not as mainstream as some, offer distinctive approaches to garment customization, pushing the boundaries of creativity.
1. Embroidery: Stitching Elegance onto Fabric
- Introduction to Embroidery: Embroidery is a timeless technique that involves stitching designs onto fabric using thread. This method adds a touch of sophistication and texture to T-shirts, making it a popular choice for creating logos, emblems, or intricate patterns.
- Process of Embroidery:
- Digitization: Designs are first digitized into embroidery machine-readable formats, translating them into a series of commands.
- Hooping and Stabilizing: The garment is hooped and stabilized to ensure even stitching.
- Machine Embroidery: The embroidery machine precisely follows the digitized pattern, stitching the design onto the fabric.
- Finishing: Loose threads are trimmed, and any excess stabilizer is removed, leaving a clean and polished embroidered design.
- Advantages of Embroidery:
- Professional Aesthetic: Embroidery imparts a professional and high-quality appearance to garments.
- Durability: The stitched design is robust and resilient, withstanding frequent washing and wear.
- Textured Feel: The raised threads create a textured feel, adding a tactile element to the design.
2. Airbrushing: A Canvas of Airborne Creativity
- The Essence of Airbrushing: Airbrushing involves using an airbrush tool to spray paint onto fabric, creating intricate and visually striking designs. This method is particularly popular for creating unique, hand-painted aesthetics.
- Airbrushing Process:
- Stencil Creation: Stencils or freehand techniques are used to guide the airbrush artist in creating the desired design.
- Color Application: Airbrush guns spray a fine mist of paint onto the fabric, allowing for smooth color transitions and gradients.
- Detailing: Artists can add fine details and shading by adjusting air pressure and paint flow.
- Advantages of Airbrushing:
- Custom Artistry: Airbrushing allows for custom, hand-painted designs, making each piece a unique work of art.
- Complex Designs: Artists can achieve intricate details and color blending that may be challenging with other methods.
- Artistic Freedom: The freehand nature of airbrushing provides artists with creative freedom and expression.
3. Spray Paint and Stencils: Street Art Inspiration
- Spray Paint Techniques: Utilizing spray paint and stencils brings an urban and street art-inspired vibe to T-shirt design. This method involves strategically placing stencils on the fabric and spray-painting over them to create bold and dynamic patterns.
- Process of Spray Paint and Stencils:
- Stencil Preparation: Stencils are either purchased or created, depending on the desired design.
- Positioning: Stencils are positioned on the garment, securing them in place.
- Spray Painting: Paint is sprayed over the stencil, creating a design on the fabric.
- Drying and Setting: Once the paint is dry, the garment is often heat-set to enhance durability.
- Advantages of Spray Paint and Stencils:
- Urban Aesthetics: This method is perfect for achieving a street art or graffiti-inspired aesthetic.
- Versatility: Artists can experiment with various stencil designs and color combinations.
- DIY Appeal: Individuals can embrace a do-it-yourself (DIY) approach to create custom, edgy designs.
4. Bleaching and Reverse Dyeing: Unleashing Art with Chemical Reactions
- Bleaching Techniques: Bleaching involves selectively removing color from a garment to create unique and visually striking designs. This method allows for intricate patterns and gradients by leveraging the chemical reactions between bleach and fabric.
- Process of Bleaching and Reverse Dyeing:
- Design Application: Either using stencils or freehand techniques, bleach is applied to specific areas of the garment.
- Color Removal: Bleach interacts with the fabric, removing color and creating the desired design.
- Neutralizing and Rinsing: The garment is neutralized to stop the bleaching process and then thoroughly rinsed.
- Advantages of Bleaching and Reverse Dyeing:
- Custom Distressed Look: Achieve a distressed or vintage appearance through controlled color removal.
- Artistic Freedom: Artists can experiment with various bleaching techniques to create intricate and personalized designs.
- Sustainability: Utilizing existing garments for bleaching promotes sustainable fashion practices.
5. Glow-in-the-Dark Printing: Illuminating Designs
- The Magic of Glow-in-the-Dark Printing: Glow-in-the-dark printing involves using specialized inks that absorb and store light, allowing the printed design to glow in low-light conditions. This technique adds an element of surprise and uniqueness to T-shirt designs.
- Application Process:
- Design Selection: Designs with specific elements meant to glow are chosen.
- Specialized Inks: Glow-in-the-dark inks are used for printing, absorbing light during exposure.
- Charging and Illumination: The printed design is charged by exposure to light and illuminates in the dark.
- Advantages of Glow-in-the-Dark Printing:
- Novelty Factor: The glow-in-the-dark effect adds a captivating and unexpected element to the design.
- Creative Expression: Designers can incorporate elements that come to life in low-light settings.
- Fun and Playful: Ideal for designs targeting a youthful or playful audience.
Choosing the Right Printing Method: A Tailored Approach
In the expansive realm of T-shirt printing, the choice of printing method depends on various factors, including design complexity, desired aesthetics, and the fabric’s characteristics. Each method explored in this segment offers a unique set of advantages, contributing to the diverse tapestry of T-shirt customization.
As you embark on your journey to create personalized garments, consider the nature of your design, the level of detail desired, and the visual impact you aim to achieve. Whether opting for the precision of CAD Heat Transfer Vinyl, the sophistication of embroidery, or the urban edge of spray paint and stencils, your choice becomes a brushstroke in the canvas of personalized fashion.
Choosing the Right Method: A Guide for Every Creator
As we navigate the diverse array of T-shirt printing methods, it becomes evident that the choice of technique is a pivotal decision in the creative process. Each method possesses unique characteristics, contributing to the overall aesthetics, durability, and cost-effectiveness of the final product. In this segment, we delve into a comprehensive guide to assist every creator in making informed decisions when selecting the right printing method.
**1. Direct-to-Garment Printing (DTG):
- Ideal for: Detailed and multicolored designs with intricate details.
- Advantages: High detail precision, full-color spectrum, suitable for small batch printing.
- Considerations: Works best on 100% cotton garments, may not be cost-effective for large quantities.
2. Screen Printing:
- Ideal for: Bold and vibrant designs with solid colors.
- Advantages: Long-lasting, vibrant colors, cost-effective for large quantities.
- Considerations: Limited color gradients, setup costs for each color.
3. Heat Transfer Methods:
- Ideal for: Small-scale, detailed designs with a variety of colors.
- Advantages: Suitable for a wide range of fabrics, intricate designs possible.
- Considerations: Durability may vary, not ideal for large production runs.
4. Dye Sublimation or All-Over Printing (AOP):
- Ideal for: Designs requiring full garment coverage and intricate patterns.
- Advantages: Seamless designs, vibrant colors, excellent for polyester fabrics.
- Considerations: Limited fabric compatibility, may not be suitable for dark fabrics.
5. Direct-to-Film Printing (DTF):
- Ideal for: Complex designs with fine details and vibrant colors.
- Advantages: High detail precision, vibrant colors, works on various fabrics.
- Considerations: Initial setup costs, may not be suitable for large quantities.
6. Embroidery:
- Ideal for: Logos, emblems, and designs requiring a textured, upscale finish.
- Advantages: Professional appearance, durable, suitable for various fabrics.
- Considerations: Limited to simpler designs, cost increases with stitch count.
7. Airbrushing:
- Ideal for: Hand-painted, artistic designs requiring a unique touch.
- Advantages: Custom artistry, intricate detailing, artistic freedom.
- Considerations: Limited for mass production, may require skilled artists.
8. Spray Paint and Stencils:
- Ideal for: Street art-inspired, bold designs.
- Advantages: Urban aesthetics, DIY appeal, versatile designs.
- Considerations: Limited for intricate details, may not be suitable for detailed logos.
9. Bleaching and Reverse Dyeing:
- Ideal for: Distressed, vintage looks, and intricate patterns.
- Advantages: Custom distressed appearance, sustainability.
- Considerations: Requires careful handling of chemicals, limited color control.
10. Glow-in-the-Dark Printing:
- Ideal for: Designs with elements meant to illuminate in low-light conditions.
- Advantages: Novelty factor, creative expression in low-light settings.
- Considerations: Limited to specific design elements, may require additional charging.
Factors to Consider When Choosing:
- Design Complexity: Detailed designs may benefit from DTG, while bold and simple designs could excel with screen printing.
- Fabric Compatibility: Consider the material of the garment, as certain methods work better on specific fabrics.
- Quantity: Large production runs may favor screen printing, while small batches may find DTG or heat transfer methods suitable.
- Artistic Freedom: For unique, handcrafted designs, methods like airbrushing or spray paint may be ideal.
Conclusion: Your Canvas, Your Choice
As a creator navigating the vast landscape of T-shirt printing, understanding the nuances of each method empowers you to make decisions aligned with your artistic vision, practical considerations, and budget. Your canvas awaits, and the choice of printing method becomes your brushstroke, contributing to the tapestry of personalized fashion.
In the concluding segment, we’ll recap the key insights explored throughout this comprehensive guide and provide a final guidepost to aid you in choosing the perfect T-shirt printing method for your individual and creative needs. Join us as we bring this artistic journey to its culmination.
Conclusion: Tailoring Creativity onto Fabric
In the vibrant world of T-shirt printing, where creativity meets fabric, we’ve embarked on a journey through an expansive palette of printing techniques. From the precision of Direct-to-Garment Printing (DTG) to the timeless craftsmanship of Screen Printing, and the artistic allure of Airbrushing, each method paints a unique stroke on the canvas of personalized fashion.
As we conclude this exploration, it’s evident that the choice of a printing method is more than a technical decision—it’s an artistic expression. Your choice becomes a bridge between imagination and reality, transforming a simple garment into a wearable masterpiece. Let’s recap the key insights we’ve uncovered:
1. Diverse Choices, Diverse Creations:
- Each printing method brings its own set of advantages and considerations.
- Whether it’s the vibrant precision of DTG or the durability of Screen Printing, there’s a method tailored to every creative vision.
2. Understanding Your Canvas:
- Fabric type plays a crucial role in determining the suitability of a printing method.
- Consider the texture, color, and composition of the garment to ensure your design flourishes.
3. Quantity Matters:
- For large production runs, Screen Printing may offer cost-effective solutions.
- Small batches can benefit from the flexibility and detail of DTG or heat transfer methods.
4. Artistic Freedom Prevails:
- Some methods, like Airbrushing or Spray Paint, offer unparalleled artistic freedom.
- Handcrafted designs find their home in these methods, adding a touch of individuality.
5. Innovation Never Ends:
- Beyond the basics, exploring unique techniques like reverse dyeing or glow-in-the-dark printing adds an innovative edge.
6. The Final Stroke – Your Decision:
- Your T-shirt is your canvas, and the choice of printing method is your brushstroke.
- Consider the intricacies of your design, the fabric you’re working with, and the quantity you’re producing.
Guiding You Forward:
- Always test your design on a sample garment before committing to a large production.
- Embrace experimentation and creativity; there’s no one-size-fits-all approach.
In the realm of T-shirt printing, creativity knows no bounds. Each stitch, each color, and each method contribute to the rich tapestry of individual expression. As you embark on your creative ventures, may your designs be bold, your fabrics vibrant, and your choices as unique as the art you bring to life.
We hope this comprehensive guide has been a beacon, illuminating the path to informed decisions and artistic fulfillment. Your journey as a creator continues, and the canvas of possibilities is vast. Tailor your creativity onto fabric, and let your designs resonate with the world. The world of personalized fashion eagerly awaits your imprint. Happy creating!
Recommendations: Finding Your Print Identity
In the diverse landscape of T-shirt printing, finding your unique print identity is an exciting journey. With an array of printing methods at your disposal, each offering distinct advantages, how do you choose the one that aligns with your creative vision? Let’s delve into some recommendations to guide you through this exploration:
1. Know Your Design:
- Understand the intricacies of your design. Does it demand fine details, vibrant colors, or a personalized touch?
- Direct-to-Garment Printing (DTG) excels in detailed and colorful designs, while Screen Printing is ideal for bold and solid graphics.
2. Embrace Versatility:
- If you’re looking for a method that can handle a variety of fabric types and colors, DTG might be your ally.
- Heat transfer methods like Vinyl or DTF also offer versatility across different fabrics.
3. Consider Quantity:
- Assess your production scale. For small batches or one-offs, DTG or heat transfer methods are efficient.
- Screen Printing becomes cost-effective for larger quantities.
4. Artistic Freedom vs. Precision:
- If your designs lean towards artistic freedom and handcrafted elements, consider Airbrushing, Spray Paint, or Tie-Dye.
- For precision and consistency, methods like DTG and Screen Printing shine.
5. Explore Beyond Basics:
- Don’t shy away from exploring unconventional methods like glow-in-the-dark printing, foil stamping, or embossing for a unique touch.
- Customizing your T-shirt with innovative techniques sets your brand apart.
6. Sample Testing:
- Before committing to a large production run, always test your design on a sample garment.
- Evaluate the look, feel, and durability to ensure the final product meets your expectations.
7. Budget Considerations:
- Different printing methods come with varying costs. Factor in your budget and long-term goals when making a decision.
- Screen Printing may offer cost advantages for bulk orders, while DTG can be economical for smaller quantities.
8. Stay Informed:
- Keep an eye on industry trends and emerging technologies. The world of T-shirt printing is dynamic, with new methods continually evolving.
- Attend trade shows, read industry publications, and stay connected with the creative community.
9. Seek Inspiration:
- Explore design platforms like Dribbble, Behance, and social media for inspiration.
- Analyze successful brands and see which printing methods align with their aesthetic.
10. Trust Your Instincts:
- Your creative instincts are invaluable. Choose a method that resonates with your vision and aligns with your brand identity.
- Your T-shirt is a canvas; let your intuition guide the brush.
In the dynamic realm of T-shirt printing, there’s no one-size-fits-all solution. Your ideal printing method is a reflection of your unique style, brand identity, and creative aspirations. Armed with these recommendations, embark on your print journey with confidence. May your T-shirts be a canvas for your imagination and a testament to your creative identity.